Once considered as an expensive way for large enterprises to stay on the top, digital transformation has become the necessity even for SMEs. All industry sectors require digital transformation to ensure growth and sustainability, and the thriving manufacturing sector is no exception! Let’s dig deep into the role of Industry 4.0 and Industry 5.0 in driving digital transformation in manufacturing.
Let’s start with key technologies that contribute to transforming the manufacturing sector digitally.
Key Technologies Driving Digital Transformation in Manufacturing
Industry 4.0 has brought radical changes in the processes of a thriving manufacturing sector. This revolutionary concept involves many technologies. Let’s understand Industry 4.0 and Industry 5.0 before looking at key technology trends that transform manufacturing processes.
What is Industry 4.0?
Industry 4.0 aka the Fourth Industrial Revolution is an ongoing automation of traditional manufacturing and industrial practices with the help of modern technologies. IoT with cloud computing, big data analytics, AI, AR, and large-scale M2M (Machine-to-Machine) communication are some of the key aspects of the Industry 4.0 concept.
What is Industry 5.0?
This is a relatively new concept and is considered a complement to Industry 4.0. It focuses on bringing sustainability and resilience in industrial production when keeping humans in the center. AI technology has a vital role to play in this concept along with robotics, IoT, and 3D printing. Other emerging trends for Industry 5.0 are digital twins and Edge computing.
Technology Trends that Set to Drive Digital Transformation in Manufacturing
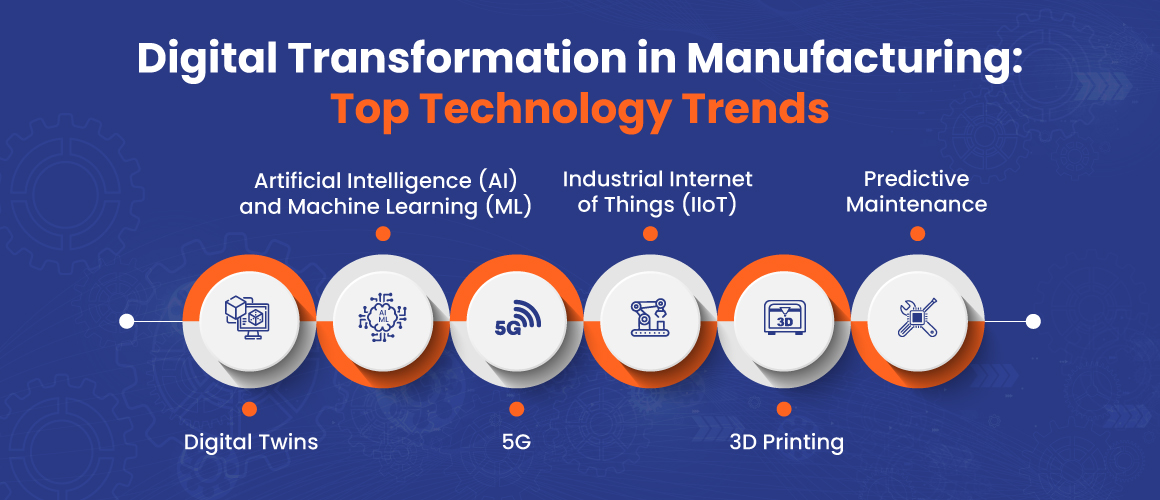
As mentioned above, all emerging trends include in both Industry 4.0 and Industry 5.0 concepts. Let’s delve into these futuristic trends-
1. Artificial Intelligence (AI) and Machine Learning (ML)
AI and ML are useful for automating tasks, improving efficiency, and predicting and preventing problems. These technologies can
- Automate quality control inspections
- Predict machine failures
- Optimize production schedules
- Contribute to developing new products
2. Industrial Internet of Things (IIoT)
The IIoT refers to the network of sensors, devices, and machines that are connected to the Internet. This allows manufacturers to
- Monitor equipment performance
- Track inventory levels
- Manage energy consumption
- Improve supply chain visibility
3. 5G
As the next generation of wireless technology, 5G offers faster speeds, lower latency, and greater capacity than previous generations. It is useful in
- Real-time quality control
- Remote machine control
- Augmented reality (AR) and virtual reality (VR) applications
4. 3D Printing
3D printing is a manufacturing process that creates three-dimensional objects from a digital model. It is being used in manufacturing to
- Produce custom medical implants
- Manufacture lightweight aerospace components
- Create rapid prototypes of new products
5. Predictive Maintenance
It is the use of data and analytics to predict when machines and equipment are likely to fail. This allows manufacturers
- Monitor the condition of machine bearings
- Track vibration levels
- Analyze oil samples for signs of wear and tear
6. Digital Twins
A digital twin is a virtual representation of a physical object or system. Digital twins are being used in manufacturing to
- Simulate new production lines before they are built
- Train workers on new equipment
- Predict the impact of design changes on product performance
As these technologies evolve and become more widespread, we can expect to see even more innovative and transformative processes in the manufacturing sector.
Examples of Successful Digital Transformations in Manufacturing
Digital transformation and the manufacturing industry are made for each other! This is simply because the majority of processes in the sector depend on big data analytics and other technologies. In the industrial revolution 5.0, manufacturers are in search of a way that combine all emerging technologies together.
Here are some successful examples of digital transformation in manufacturing.
Data Management
The manufacturing industry is one of the biggest producers of big data as machines and workers generate data constantly. Manufacturers and their customers need solutions to manage and analyze this data to extract valuable insights. A digital transformation strategy in manufacturing includes big data solutions.
Predictive Maintenance
When machines break down, it can disrupt workflows and the entire supply chain. Manufacturers need AI and data analytics tools to enable predictive maintenance, which helps them foresee and address potential problems before they cause breakdowns or big damage in the production process.
Supply Chain Resilience
Supply chain disruptions often occur outside of a manufacturer's control. However, digital transformation can help manufacturers navigate these uncertainties and act as a cushion or safety net. Manufacturers can use digital technology to create solutions to reduce the impact of supply chain disruptions.
It is fair to mention that digital transformation can help manufacturers address their unique needs and create the digital experiences that will be the future of manufacturing.
However, it is necessary to overcome some challenges and follow the best practices of digital transformation to leverage the benefits of Industry 4.0 and Industry 5.0.
Challenges and Best Practices for Implementing Digital Transformation in Manufacturing
Here we mention big challenges in the way of digital transformation in the manufacturing sector-
Unclear Vision
Many manufacturing companies lack a clear vision for what they want to achieve with digital transformation. This can make it difficult to identify the right technologies and implement them effectively.
Employee Resistance
Digital transformation can be disruptive, and it can be difficult to get all employees on the same page. It is, therefore, important to communicate the benefits of digital transformation and to provide them with training.
High Investment
The initial upfront costs of digital transformation can be significant. This can be a barrier for smaller manufacturing companies. However, there are ways to reduce the costs, such as implementing it in phases.
No Expertise
Many manufacturing companies lack the technical expertise needed to implement digital transformation effectively. This can be a major challenge. It is important to give your employees the necessary training.
You need to follow the best practices to overcome these challenges effectively. Best practices for implementing digital transformation in the manufacturing sector include-
Starting with Clarity
A clear vision and objectives for your manufacturing company are necessary before initiating digital transformation activities. Once you have a clear understanding of your goals, you can start to make a roadmap.
Focus on Technologies
Don't just implement new technologies for the sake of it. You can take the help of a digital transformation consultant to choose technologies that will help you achieve your specific goals and objectives.
Invest in Analytics
Big Data Analytics can play a crucial role in digital transformation. Manufacturers need to be able to collect, manage, and analyze data to make informed decisions about their businesses.
Involve Your Employees
Digital transformation is not just about technology. It's also about people. You must engage your employees and get them on board with the transformation process to ensure success.
Measure Your Results
It's essential to track your progress and measure the results of your digital transformation project. This will help you make the necessary adjustments quickly.
You can make your industry ready for the future by implementing these best practices of digital transformation.
Future of Digital Transformation in Manufacturing
When we think of the future of digital transformation we need to consider both Industry 4.0 and Industry 5.0 along with the use of automation, cyber-physical systems and the IoT to build smart factories where sustainability and resilience remain at the core. Digital transformation has a lot of potential with evolving technologies. It is interesting to see how manufacturers can get all the benefits of Industry 4.0 and 5.0 for bringing disruptive changes.
How Manufacturers can Stay Ahead of the Curve in Digital Transformation
If you want to stay ahead of the curve through digital transformation, here are five top tips you can keep in mind-
- Develop a cohesive digital strategy in line with your business model and objectives
- Invest in data and analytics to gain insights into your operations and customers
- Break down silos and integrate business functions to gain the full benefits of transformation
- Create a culture of innovation and empowerment, and invest in upskilling your workforce
- Ensure easy access to tools and data to enable your employees to drive digital transformation
Apart from these tips, it is essential to find the right digital transformation company for your manufacturing company.
Conclusion
Evolving technologies including AI, IoT, and big data analytics can make a big impact on your manufacturing processes. You can make the most of these technologies to increase resilience and sustainability by implementing digital transformation effectively. Hope this guide will help you succeed in your digital transformation initiative.
At Silver Touch Technologies, we focus on integrating technological advancements in tailored manufacturing solutions. Our expertise in developing high-end manufacturing software can help you bring digital transformation by leveraging the revolutionary concepts of Industry 4.0 and Industry 5.0. Do you want to know the benefits of Industry 4.0 and 5.0 for your company?
FAQs
What is digital transformation in manufacturing?
Digital transformation in manufacturing is the integration of advanced digital technologies into manufacturing operations to enhance efficiency, effectiveness, and sustainability. This involves using technologies like AI, IoT, and big data analytics to automate tasks, optimize production, and predict and prevent issues.
What are the benefits of digital transformation in manufacturing?
Digital transformation revolutionizes manufacturing by increasing efficiency, improving product quality, reducing costs, increasing agility, and enhancing customer satisfaction.
What are the challenges of digital transformation in manufacturing?
Challenges include the cost of implementing new technologies, the need for new skills and training, cultural resistance to change, and the need to integrate new technologies with existing systems.
How can manufacturers overcome the challenges of digital transformation?
Develop a clear vision, invest in the necessary resources, engage employees in the transformation process, and measure the results of digital transformation efforts.
What are the key technologies driving digital transformation in manufacturing?
The key technologies driving digital transformation in manufacturing include AI/ML, IIoT, 5G, 3D printing, and digital twins.